Textile Machinery in the Garment Industry
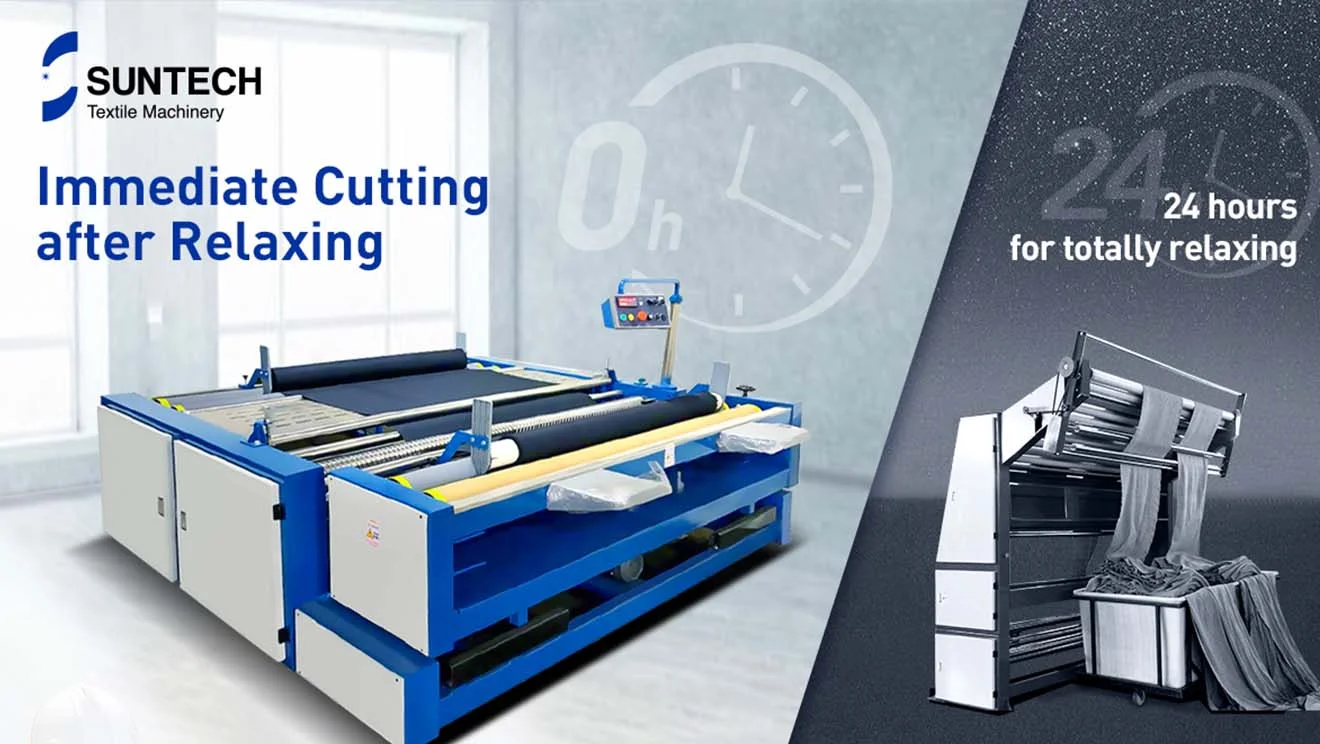
Textile machinery automation plays a pivotal role in the garment industry, extending far beyond the headlines. Its impact is profound behind the scenes, silently revolutionizing the entire clothing manufacturing process. Particularly in medium- to large-scale garment factories, automated technology drives the crucial tasks of fabric relaxing, cutting, and fusing, which traditionally demanded substantial physical labor.
Automatic fabric relaxing machines outperform manual labor in terms of speed and efficiency. When compared to manual relaxing, equipment for automatic fabric relaxing offers numerous advantages. One of the key benefits is a reduction in the workforce required for the relaxing process. In manual relaxing, two individuals are typically needed to pull on each side of the fabric, ensuring even spreading without folds or twists. By employing a fabric-relaxing machine, other workers can be freed up to perform additional tasks or utilize their labor more flexibly. The machine accelerates and streamlines the relaxing process, outpacing human capabilities and significantly speeding up the overall manufacturing process. Consequently, enhanced productivity and more competitive pricing can greatly benefit the apparel industry.
Employing an automatic fabric relaxing machine significantly reduces the risk of worker injuries. The traditional method requires workers to stand at a table and exert physical force to tug on the fabric, leading to potential strains and long-term damage. By entrusting the relaxing operation to the machine, workers are relieved of this physically demanding task, thereby minimizing the risk of injury and enhancing overall working conditions.
Among the latest advancements, the multi-roll woven fabric relaxing machine surpasses its single-layer counterparts, representing the pinnacle of innovation. Capable of simultaneously relaxing six or more rolls of fabric, this heavy-duty machine proves ideal for applications involving protective clothing, PPE items, and larger woven materials. Its efficiency is increased sixfold, revolutionizing productivity.
Furthermore, the newest spreader available in the market features automatic work order sheet entry, report generation, and remote production monitoring capabilities. This eliminates the need for frontline employees to manually create work orders, while also enabling real-time control over production progress. Such advancements streamline operations and empower workers with efficient tools for enhanced productivity and monitoring.
Utilizing autonomous fabric-relaxing machines yields numerous advantages, including reduced labor costs, enhanced speed and efficiency, and improved working conditions.
Following the fabric relaxing process, fabric cutting becomes a crucial stage where precise shapes required for garment designs are cut out from the spread fabrics. This step holds significant importance as garments made from inaccurately cut fabrics may result in ill-fitting or unwearable products. In cases of severe cutting errors, manufacturers are compelled to discard the miscut fabrics and begin anew.
Manual fabric cutting involves a factory worker following an outline drawn or overlaid on the top fabric layer. While this method may suffice for low-output manufacturers, it falls short in meeting the demands of larger suppliers. Moreover, human errors are prone to occur, as workers can mistakenly deviate from the lines and waste perfectly good fabric. Additionally, the risk of accidental injuries looms, particularly when workers are fatigued after long hours. Therefore, manual cutting poses liabilities for manufacturers.
In contrast, automatic cutting machines excel in efficiently and accurately cutting through multiple fabric layers. These machines incorporate automatic blade sharpening, ensuring precision and quality even when handling substantial fabric volumes. Automated cutting not only enhances productivity but also improves the working environment by reducing physically demanding and inefficient tasks that employees would otherwise have to undertake.
The remarkable advantage of an automatic cutting machine lies in its ability to seamlessly integrate and connect data, which brings significant value and opens up new possibilities for development once the factory embraces digital transformation.
The garment industry has undergone a remarkable transformation through the integration of automated machinery, resulting in enhanced efficiency, accuracy, and sustainability throughout the entire production line. By minimizing the need for excessive personnel, reducing human error, and curbing fabric wastage, automation has successfully lowered costs, prevented order delays, improved worker safety, and reduced environmental impact. Manufacturers can now produce garments of superior quality and effectively meet the demands of the global market.
Comments
Post a Comment